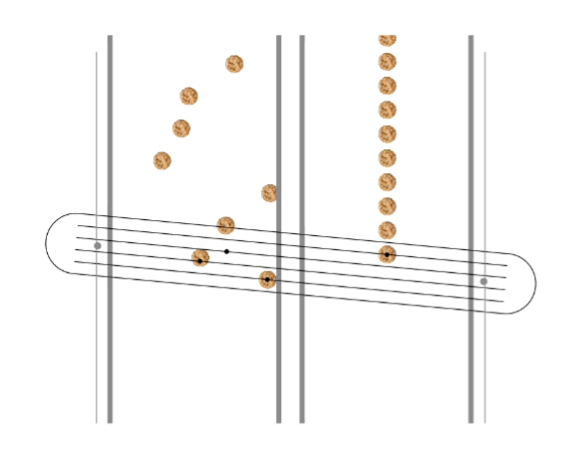
Play Video
Compact and fast production lines
The carrier thus resembles a railroad station through which the pick heads move like trains. They can travel simultaneously on different rails side by side in one direction, or in opposite directions, without any risk of collision. Secondly, the entire main beam is not only movable on a parallel/transverse basis, but is also rotatable horizontally thanks to rotating suspensions. These two innovations – multiple pick heads and rotating suspension – allow the robot to operate at two points simultaneously. One of the pick heads can even remain in one place while another one moves to several targets in succession.